Silicone is a versatile and widely used material across industries, valued for its excellent heat resistance, chemical stability, and flexibility. It comes in two primary forms: liquid silicone and solid silicone. Each type has unique properties and applications, making it essential to understand their differences to select the right material for your needs.
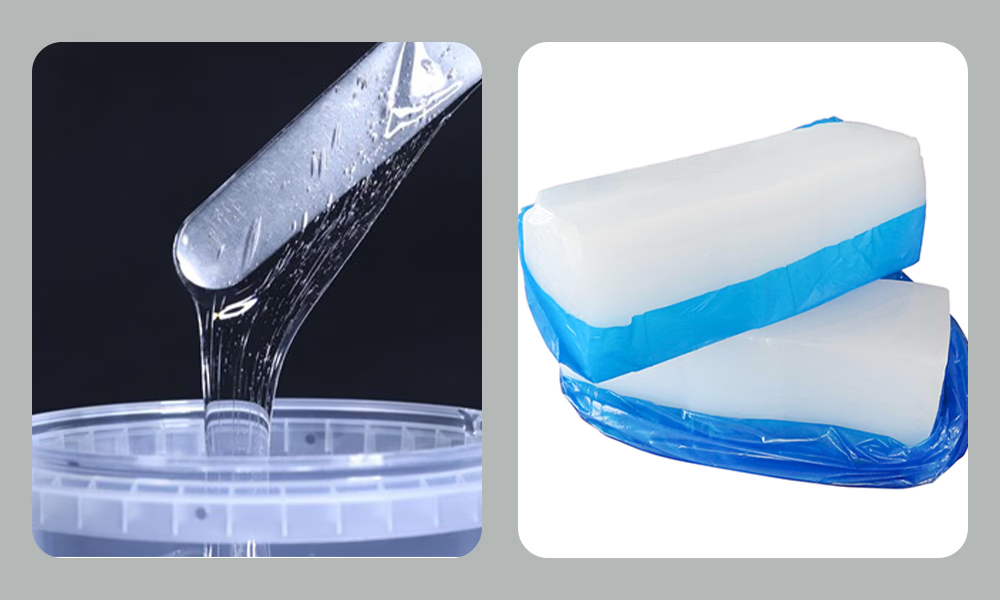
Physical State and Appearance
Liquid Silicone:
- Exists in a fluid form at room temperature.
- Features low viscosity, allowing it to flow easily and fill intricate molds.
- Can be poured, injected, or dispensed, offering adaptability in manufacturing.
- Image Suggestion: A photo of liquid silicone being injected into a mold during the liquid injection molding (LIM) process, showcasing its fluidity and ability to conform to complex shapes.
Solid Silicone:
- Comes in a solid form, available as sheets, blocks, or pre-formed shapes.
- Has a more rigid structure but retains flexibility based on its formulation.
- Appearance varies from smooth and glossy to textured surfaces.
- Image Suggestion: A photo of a solid silicone product, such as an automotive gasket or a medical catheter, highlighting its rigidity and practical applications.
Processing and Manufacturing
Liquid Silicone:
- Processed via liquid injection molding (LIM), where it’s injected into a mold under high pressure and cured with heat.
- Ideal for high-precision, complex parts and large-scale production.
Solid Silicone:
- Processed using techniques like compression molding or transfer molding.
- Can also be machined, cut, or fabricated into custom shapes.
Mechanical Properties
Liquid Silicone:
- Typically has lower hardness, ranging from 20-60 Shore A.
- Offers excellent flexibility and elongation (e.g., up to 600% elongation at break).
- Perfect for stretchable applications like medical tubing or rubber bands.
Solid Silicone:
- Available in a wide hardness range, from soft (20 Shore A) to hard (70 Shore A or higher).
- Boasts superior tear resistance (e.g., tear strength up to 40 N/mm) and abrasion resistance.
- Suited for applications requiring durability, such as automotive seals or industrial parts.
Chemical Resistance
Both types exhibit good chemical resistance, but their strengths differ slightly:
Liquid Silicone:
- More resistant to oils and solvents due to its specific formulation.
Solid Silicone:
- Better suited for prolonged exposure to harsh chemicals like strong acids (e.g., sulfuric acid) or alkalis.
- Its stable structure enhances durability in aggressive chemical environments.
Applications
Liquid Silicone:
- Widely used in the medical field for products like catheters and tubing (e.g., Stryker’s medical devices).
- Employed in electronics for potting and encapsulating components.
- Popular in baby products like pacifiers due to its softness and safety.
Solid Silicone:
- Common in the automotive industry for engine gaskets and seals .
- Used in construction for weatherstripping and roofing membranes.
- Found in cookware, such as silicone baking mats, thanks to its heat resistance and non-stick properties.
Conclusion
Liquid silicone and solid silicone each bring distinct advantages to the table, depending on the application. By understanding their differences in physical properties, processing methods, and performance, manufacturers can make informed decisions to select the best silicone material for their specific needs.