Customised LSR Overmolding Services
Rapid overmolding and insert molding capabilities to produce parts from a range of thermoplastic and liquid silicone rubber materials for on-demand production, bridge tooling, pilot rune, and rapid prototyping needs. With the utilization of aluminum molds that offer cost-effective tooling, prototypes and on-demand production parts may be produced in as fast as 15 days.
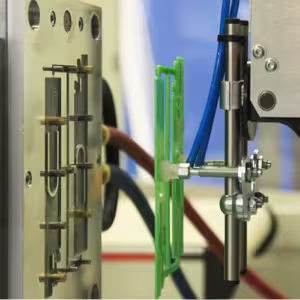
Start A New LSR Overmolding Project
STEP | STP | SLDPRT | IPT | PRT | SAT files
- All uploads are secure and confidential.
/01
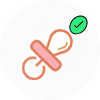
High Quality Parts
Owing certified factories, conducting in-process inspections and dimensional verification after production, guarantee the custom molded parts are consistent in quality regardless of the complex shape with high precision.
/02
Fast Lead Time
With certified domestic factories and a strong supply chain system, we accelerate the product development cycle and bridge the production of your overmolded parts as fast as possible.
/03
Engineering Support
Working with our experts having 10+ years of experience in the silicone overmolding industry, efficiently complete a turnaround from prototyping to production.
What is Silicone Overmolding?
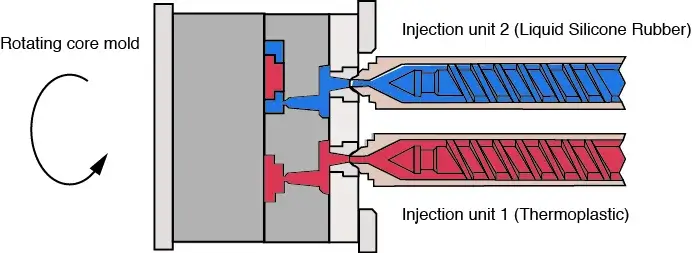
Silicone Overmolding, also named Rubber Overmolding, Liquid Silicone Rubber(LSR) Overmolding, is a multi-step injection molding process where two or more components are molded over top of one another. Overmolding is sometimes referred to as two-shot molding because it is a two-step process.
The common secondary molding material concludes PC, PPSU, PA + GF, PBT, etc., All are thermoplastic materials with high-temperature resistance. While common overruled material is silicone (high-temperature vulcanization silicone or low-temperature vulcanization silicone) or liquid silicone rubber (LSR). Compared with the assembly or bonding parts, the silicone overmolding parts have better quality.
LSR Overmolding Process
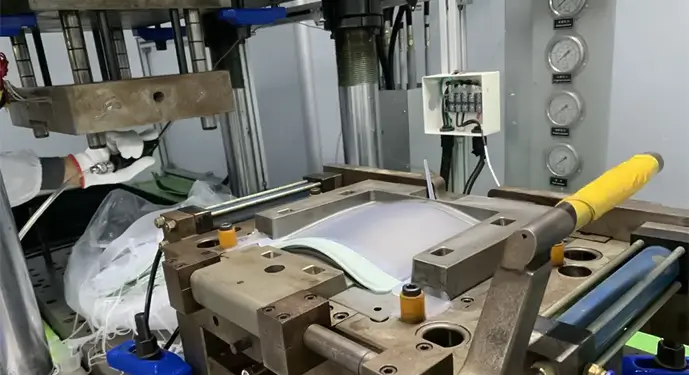
Two-Shot Over Molding
Crucial for mass production, involves machining, and assembling durable molds from steel or aluminum to ensure precise and repeatable part geometries.
- Aluminum and steel injection mold.
- Achieves detailed geometries.
- Ideal for mass production.

Liquid Silicone Rubber to Plastics
Overmolding improves product functionality and aesthetics by fusing different materials into one part, adding features like soft grips and multi-color designs for enhanced usability
- Improves strength and lifespan.
- Combines different materials seamlessly.
- Offers color and texture options.
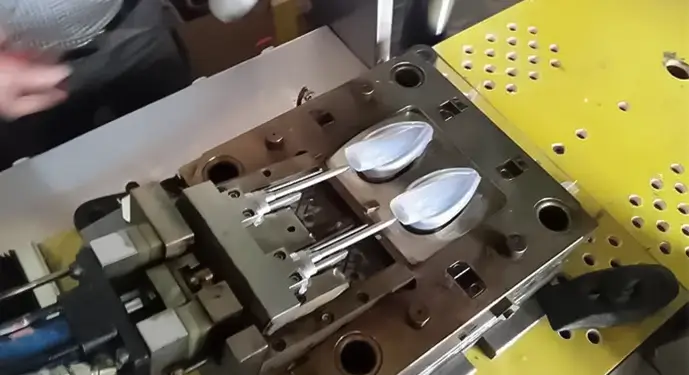
Liquid Silicone Rubber to Metals
Insert molding integrates metal or other materials into plastic parts during molding, enhancing strength and reducing assembly time for components with embedded features.
- Reduces assembly steps.
- Enhances component durability.
- Lowers production expenses.
Silicone Overmolding Tooling Solutions
Prototyping
Rapid Tooling
Get easy design feedback and validation through superior quality prototype tooling. Create small batches of plastic molded parts with excellent injection molding prototypes. We excel at manufacturing prototype molds within days to ensure you perform functional tests and validate market interest.
Production
Production Tooling
We create high-quality production molds for high-volume plastic parts production. With high-strength, durable tool steel material, our production tooling is suitable for producing hundreds of thousands of parts. We can vary materials and construction methods according to your unique requirements.
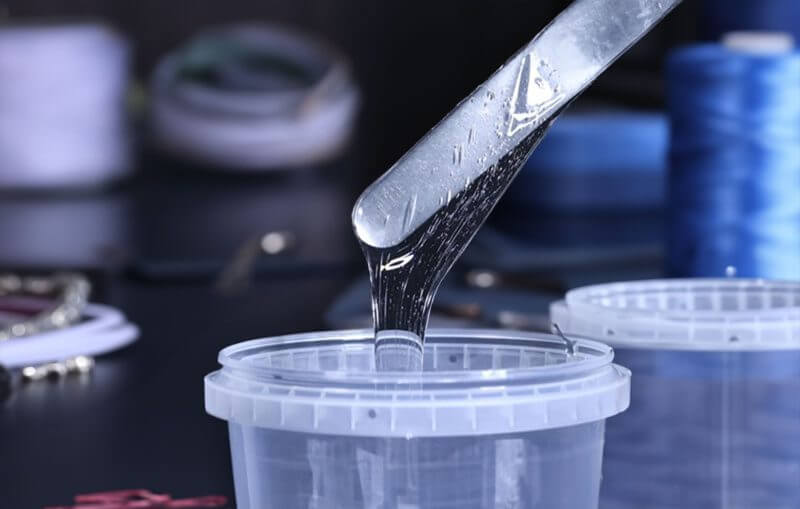
Liquid Silicone Rubber Materials
- Standard Silicone (30, 40, 50, 60, and 70 durometers)
- Medical-Grade Silicone
- Optical-Grade Silicone
- Fluorosilicone (fuel and oil resistant)
Silicone Overmolding Finishes
SPI Finishes
As Molded
Other Mold Texturing
Silicone Overmolding Design Tips
- Wall thicknesses between 0.060" to 0.120" (1.5 mm-3 mm) generally provide the best bonding.
- Keeping radii between 0.020" or 0.5mm minimum in corners reduces localized stresses.
- If the part requires the use of thick TPE sections, they should be cored out to minimize shrinkage problems, reduce the part weight and lower cycle time.
- Avoid deep or un-ventable blind pockets or ribs in your design.
- Use gradual transitions between wall thickness to reduce or avoid problems with flow (back fills, gas traps, etc.)
- Overmolding needs mechanical or chemical bonding to the substrate, so your overmold material choices should enable this.
Silicone Overmolding Capabilities
Standards | Description |
---|---|
Maximum Part Size | 200×400×100mm 7.87×15.75×3.94 in. |
Manimum Part Size | 2×2×2mm 0.08×0.08×0.08in |
Substrate Wall Thickness | From 0.5 to 3mm From 0.20 to 0.12 in. |
Tolerance | +/- 0.025 mm +/- 0.00098 in. |
Radii | 0.1mm 0.0039in. |
Depth | 100mm from the parting line 3.94 in. from the parting line |
Mold Validation | Provide T0, T1, T2 samples before mass production |
Inspection and Certification Options | First Article Inspection, ISO 9001, ISO 13485 |
Lead Time | From mold making to sample delivery: 15-21 business days |
Silicone Overmolding for Various Industries
With ShengHui, benefit from custom overmolding that adapts seamlessly to the diverse requirements of different industry sectors, ensuring optimal results.
Advantages of LSR Overmolding
LSR overmolding enhances product durability and functionality by integrating different materials, offering improved grip, aesthetics, and cost-effective assembly.
- Improved Design and Creation of Custom Silicone Parts: Overmolding capabilities ensure the creation of custom silicone-silicone or metal-silicone product combinations with a high dimensional quality.
- Better Product Performance: Overmolded parts are of excellent quality because of their two-material advantage for various applications.
- Increased Shelf and Aesthetic Appeal: The overmolding process can be optimized with many materials and surface treatment processes to improve the aesthetic quality of the product.
- Lower Production Costs: Since overmolding eliminates post-assembly phase of production, it speeds up the production process and reduces overall manufacturing cost.
Applications of LSR Overmolding
The LSR overmolding process is compatible with a wide variety of materials, ranging from plastics to metals. This process helps produce custom prototypes and production parts for various applications depending on your requirements. Several industries find valuable uses for overmolding services.
- Lower Production Costs: Since overmolding eliminates post-assembly phase of production, it speeds up the production process and reduces overall manufacturing cost.