On-Demand Manufacturing
On-demand production helps meet your needs more effectively, and stay competitive in your industry. Lowered manufacturing costs, increased flexibility.
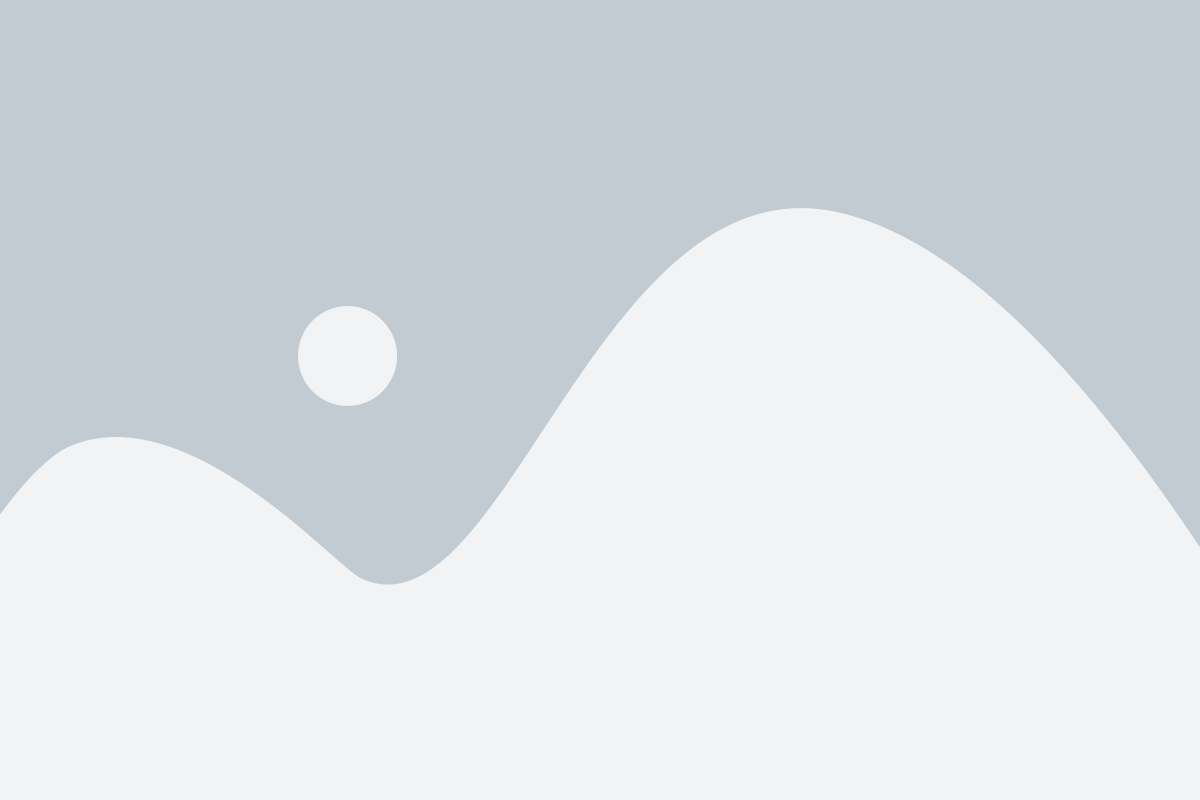
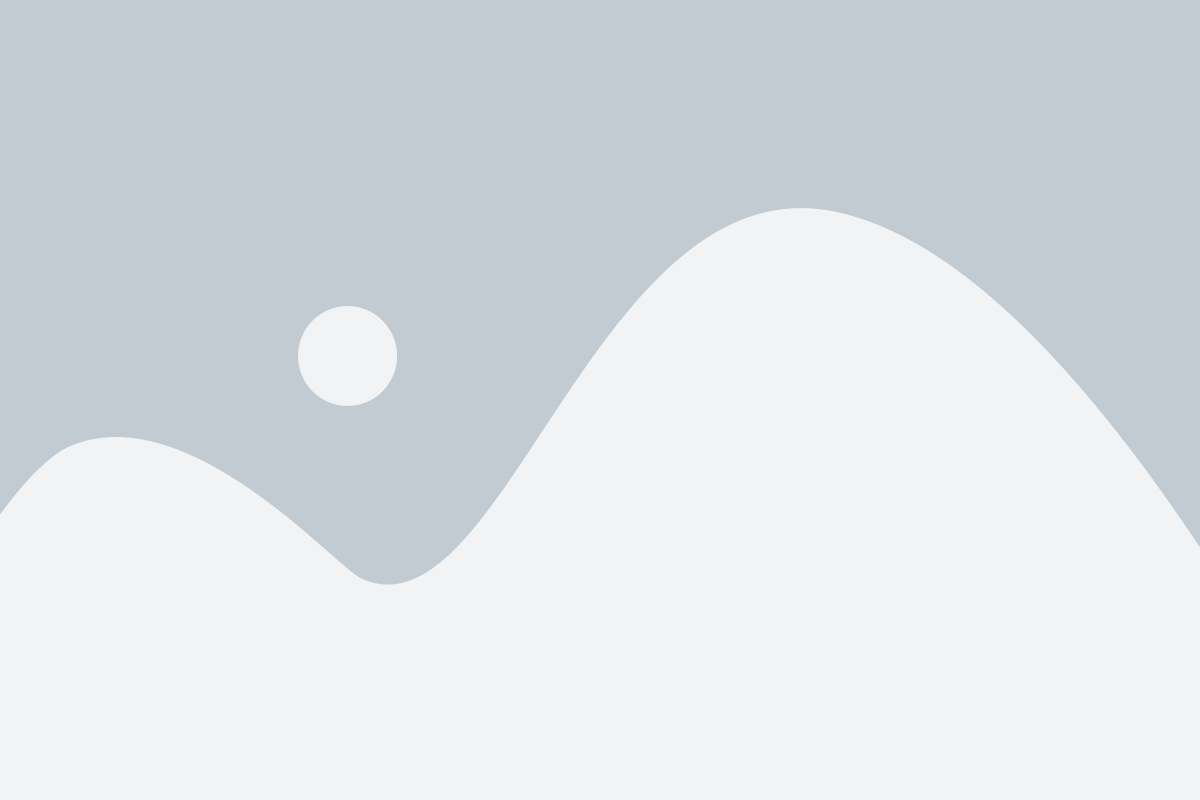
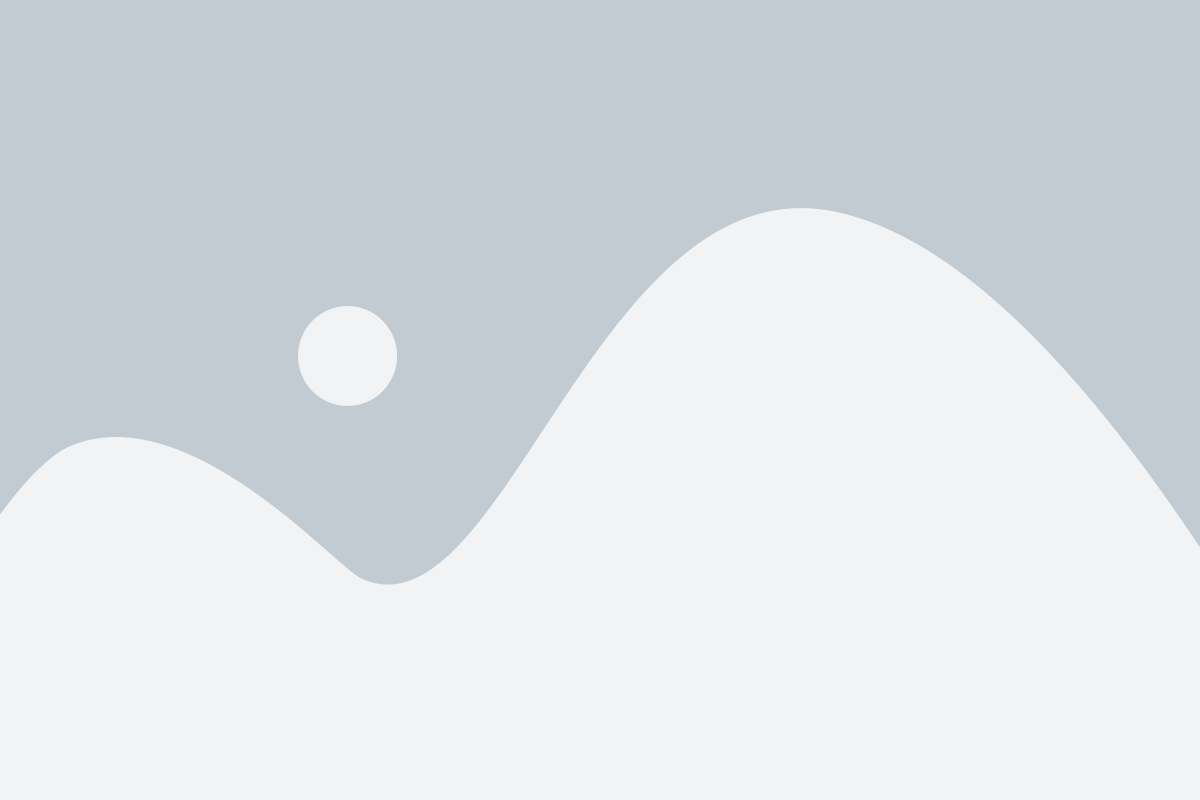
Start A Custom Production Quote
STEP | STP | SLDPRT | IPT | PRT | SAT files
- All uploads are secure and confidential.
On Demand Production with ShengHui
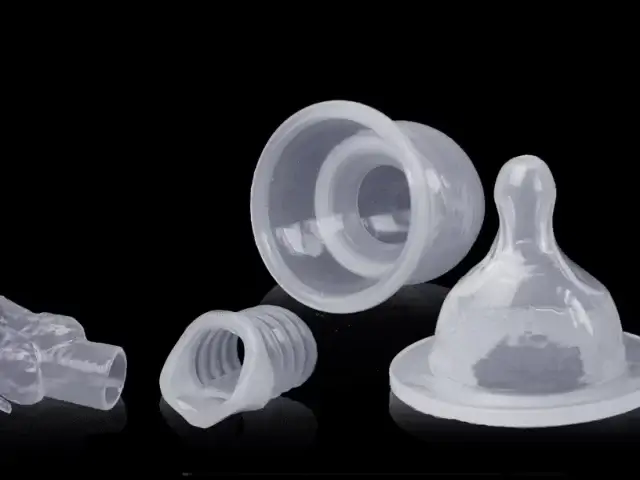
ShengHui got you covered on all on demand manufacturing needs. Based on our years of experience and expertise, we will efficiently execute all your projects concerning on demand production. Thanks to an unlimited supply chain network of workshops for different manufacturing techniques, you can rest assured that you’re getting the fastest delivery of the best products at an amazing wholesale price. Moreover, our experienced engineers and experts will proffer the best solutions and design modification suggestions to ensure you have the finest end product.
Our On-Demand Production Services
LSR lnjection Molding
Silicone injection molding is the process of injecting liquid silicone rubber (LSR) under pressure into a mold cavity, where it fills and cures to form the final product. Unlike thermoplastic or thermosetting polymers, silicone undergoes a curing process during molding, solidifying into its final form through a chemical reaction triggered by heat.
Type
- Mold cavity tolerances
- Standard lead time
- Part to part repeatability
- Production grade
Tolerance
- ±0.05 mm
- 15 business days or less
- ±0.1 mm
- 1-100,000 cycles
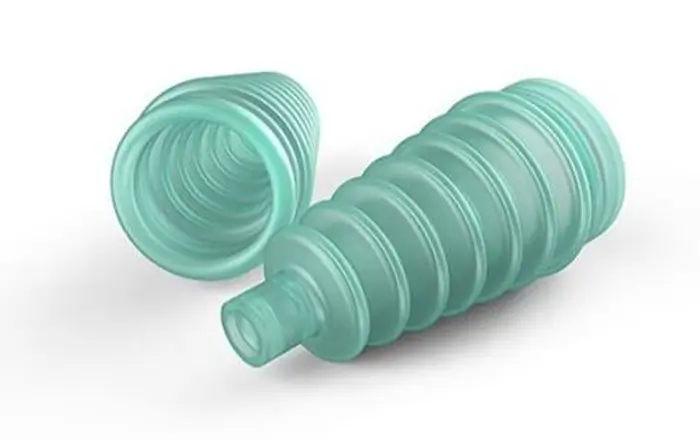
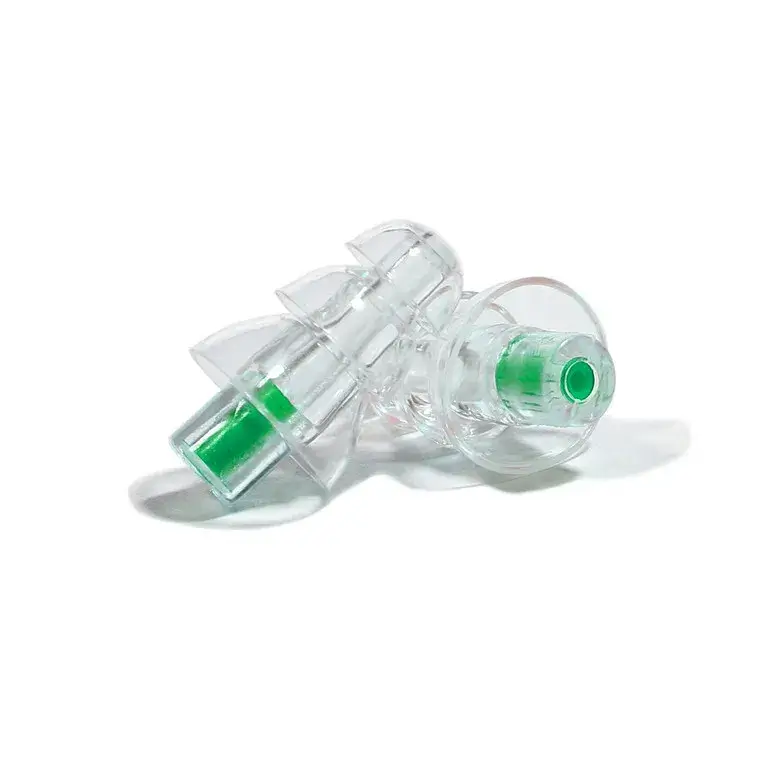
LSR Overmolding Molding
Silicone overmolding is a manufacturing process where liquid silicone rubber (LSR) is molded over another material, such as plastic, metal, or even another silicone part. This process creates a strong bond between the silicone and the underlying substrate, resulting in a single integrated product. Silicone overmolding is commonly used in applications requiring enhanced grip, waterproofing, insulation, or cushioning. The versatility of silicone makes it ideal for use in medical devices, electronics, automotive parts, and consumer products, where durability and performance are critical. Overmolding also helps in adding ergonomic features and improving the aesthetic and tactile feel of the product.
Type
- Mold cavity tolerances
- Standard lead time
- Part to part repeatability
- Production grade
Tolerance
- ±0.05 mm
- 15 business days or less
- ±0.1 mm
- 1-100,000 cycles
Silicone Dripping Dispensing Molding
Silicone dripping dispensing molding is a process where liquid silicone is precisely dispensed in controlled droplets onto a substrate or mold using automated machinery. This technique is commonly used to create intricate designs, logos, seals, or coatings on a variety of surfaces, such as textiles, electronics, or other silicone components. The dispensing process allows for high accuracy and consistency, making it ideal for complex or small-scale applications. Once the silicone is applied, it undergoes a curing process, either through heat or UV exposure, to solidify and bond to the substrate. This method is widely used in industries such as fashion, electronics, automotive, and medical devices, providing enhanced functionality, such as improved grip, insulation, or decorative elements.
Type
- Mold cavity tolerances
- Standard lead time
- Part to part repeatability
- Production grade
Tolerance
- ±0.05 mm
- 15 business days or less
- ±0.1 mm
- 1-100,000 cycles
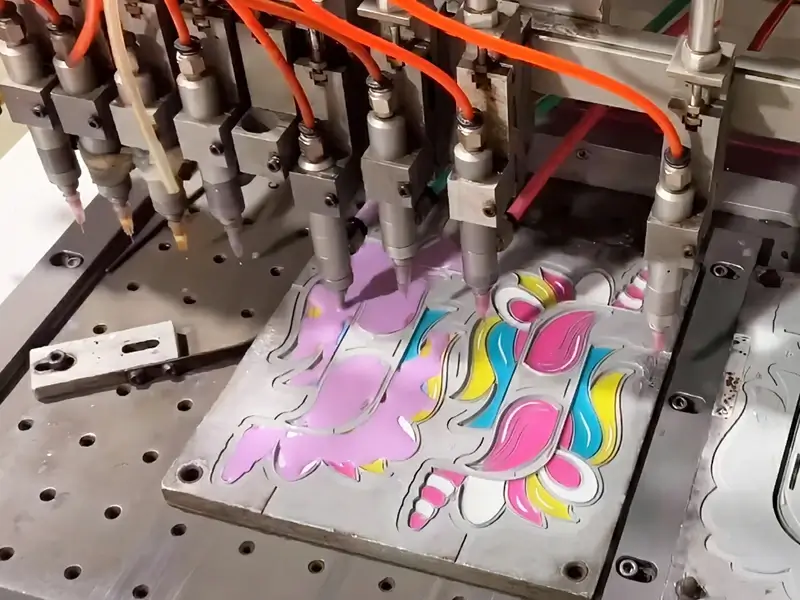
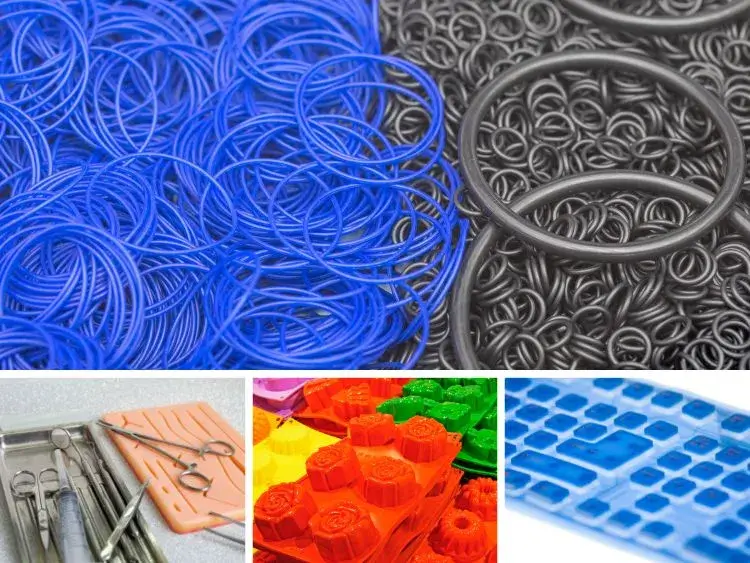
Silicone Compression Molding
Silicone compression molding is a manufacturing process where a pre-measured amount of silicone material is placed into an open mold cavity. The mold is then closed, and pressure and heat are applied to shape the silicone into the desired form. The combination of heat and pressure cures the silicone, allowing it to solidify and take on the mold’s exact shape. This process is especially effective for producing high-quality, durable parts with complex geometries or large surface areas. Silicone compression molding is commonly used for manufacturing seals, gaskets, medical devices, and other components that require excellent durability, flexibility, and resistance to extreme temperatures. It is a cost-effective method for producing both small and large quantities of silicone parts.
Type
- Mold cavity tolerances
- Standard lead time
- Part to part repeatability
- Production grade
Tolerance
- ±0.05 mm
- 15 business days or less
- ±0.1 mm
- 1-100,000 cycles
Why Choose Us
/01
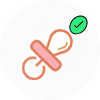
High Quality Parts
We use high-quality input materials and maintain a high level of process stability to ensure reproducibility. We strive for continuous improvement to improve our manufacturing of goods, processes, and delivery capability.
/02
Fast Lead Time
We have a state-of-the-art in-house production supply chain and staff strength that helps us meet and exceed your expectations on delivery time and quantity. We ensure that all our deliveries are within schedule.
/03
Engineering Support
Our team of refined and experienced experts is always available for professional advice and recommendation on your orders, improvements, and preferences.