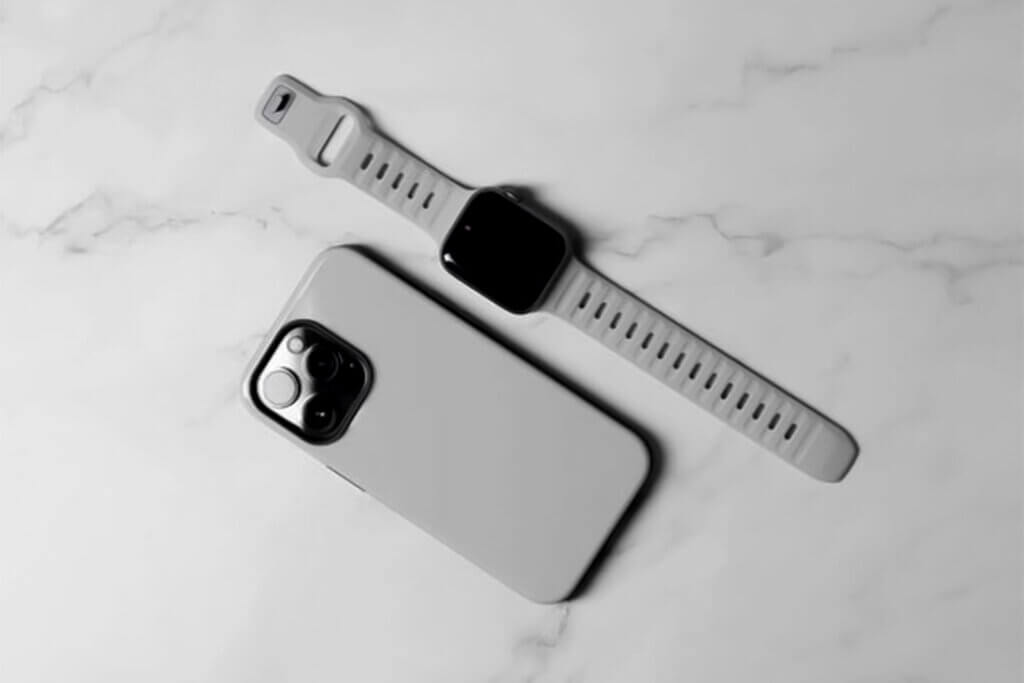
In the large family of injection molding processes, liquid silicone rubber injection molding occupies an important position with its unique properties and advantages. It provides an efficient solution for manufacturing various soft, durable, and precise products and is widely used in many industries. Next, let’s explore the mysteries of liquid silicone rubber injection molding in depth.
Introduction to Liquid Silicone Rubber
Liquid Silicone Rubber (LSR for short) is a kind of polymer material with a special molecular structure. Its molecular main chain is composed of alternating silicon and oxygen atoms, and the side chains are connected with organic groups. This unique structure endows it with a series of excellent properties.
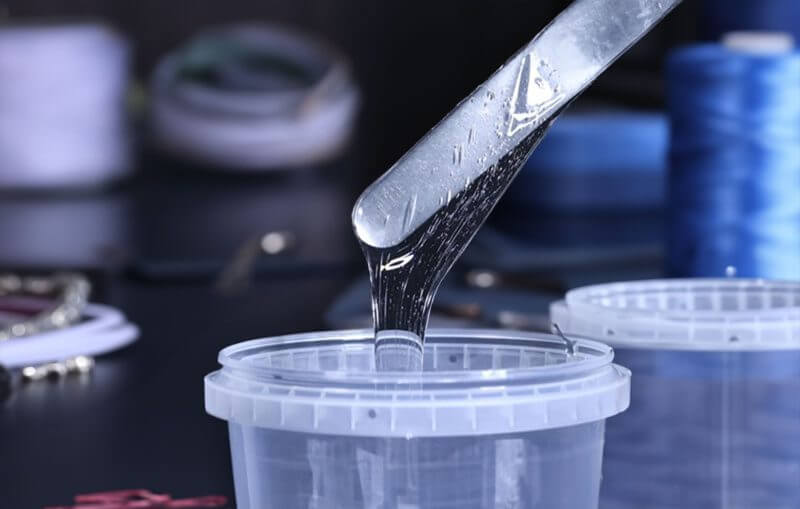
Characteristics of Liquid Silicone Rubber
- Excellent Temperature Resistance: It can maintain stable physical properties in the extreme temperature range from -60°C to 250°C. Whether in the cold polar environment or the high – temperature industrial production scene, it can work normally.
- Outstanding Flexibility: It has extremely high elasticity and can recover to its original state within a large deformation range, and is not prone to permanent deformation. This makes it perform well in manufacturing products that need to be bent and stretched frequently.
- Good Chemical Stability: It has resistance to most chemical substances and is not easily corroded by chemical reagents such as acids and alkalis. It can be used to manufacture products that come into contact with chemicals.
- Excellent Biocompatibility: It has good compatibility with human tissues and body fluids, is non – toxic, odorless, and non – irritating. It is widely used in the medical field, such as manufacturing artificial organs, medical catheters, etc.
- High Transparency and Easy Colorability: It has high transparency in its natural state and is also easy to add various pigments for coloring, which can meet the appearance requirements of different products.
What is Liquid Silicone Rubber Injection Molding?
Liquid silicone rubber injection molding is a processing technology that injects liquid silicone rubber raw materials into the mold cavity through an injection molding machine, and forms products with specific shapes and sizes after heating and curing. It is an efficient and precise molding method that can achieve large – scale production.
How Does Liquid Silicone Rubber Injection Molding Work?
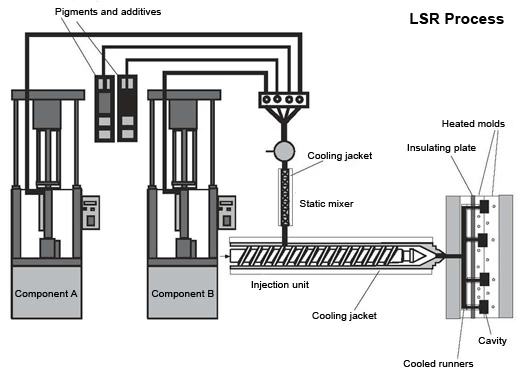
- Mold Preparation: First, according to the product design requirements, a high – precision mold is manufactured. The mold is usually made of steel and undergoes precision processing and heat treatment to ensure its dimensional accuracy and surface quality.
- Raw Material Preparation: The base rubber and curing agent of liquid silicone rubber are mixed evenly in a certain proportion. At the same time, additives such as pigments and fillers can be added as needed to adjust the performance and color of the product.
- Injection Process: The well – mixed liquid silicone rubber is injected into the mold cavity under high pressure through the screw or plunger of the injection molding machine. The parameters such as pressure, speed, and temperature of the injection molding machine can be precisely controlled according to the product requirements.
- Curing Stage: The liquid silicone rubber injected into the mold cavity begins to cure under the action of heating and gradually transforms into a solid with certain strength and shape. The curing time depends on the thickness, size of the product, and the formula of the silicone rubber, generally ranging from tens of seconds to a few minutes.
- Demolding and Post – processing: After curing is completed, the mold is opened and the product is removed from the mold. The demolded product may need to undergo some post – processing, such as trimming flash, polishing, surface treatment, etc., to improve the appearance quality and performance of the product.
Advantages of Liquid Silicone Rubber Injection Molding
- High Precision and High Repeatability: It can produce products with high dimensional accuracy and good surface quality, and maintain stable quality in large – scale production. The consistency and repeatability of products are very high.
- Complex Shape Molding Ability: Due to the good fluidity of liquid silicone rubber, it can fill the complex mold cavity and realize the molding of various complex – shaped products without the need for secondary processing.
- Efficient Production: The injection molding process has a high degree of automation and a short production cycle, and can realize large – scale continuous production, improving production efficiency and reducing production costs.
- High Material Utilization Rate: In the injection process, liquid silicone rubber can fully fill the mold cavity, reducing the generation of waste and improving the material utilization rate.
- Good Physical Properties: The products made have excellent flexibility, temperature resistance, chemical stability, and biocompatibility, and can meet various application requirements.
Liquid Silicone Rubber Injection Molding Equipment
- Injection Molding Machine: It is the core equipment of liquid silicone rubber injection molding. It is responsible for injecting the well – mixed liquid silicone rubber into the mold cavity. The performance of the injection molding machine directly affects the quality and production efficiency of the product.
- Mold: The mold is a key component that determines the shape and size of the product. It needs to be precisely manufactured according to the product design requirements. The structural design and manufacturing accuracy of the mold have an important impact on the quality and production efficiency of the product.
- Mixing Equipment: It is used to evenly mix the base rubber, curing agent, and other additives of liquid silicone rubber to ensure the stable performance of the product.
- Heating and Cooling System: During the injection molding process, the mold needs to be heated and cooled to realize the curing of liquid silicone rubber and the demolding of the product. The performance of the heating and cooling system directly affects the quality and production efficiency of the product.
Applications of Liquid Silicone Rubber Injection Molding
- Medical Field: Due to its good biocompatibility, it is widely used in the manufacture of medical equipment, medical devices, artificial organs, etc., such as syringes, infusion tubes, heart pacemaker housings, etc.
- Automotive Industry: It is used to manufacture automotive seals, shock absorbers, interior parts, etc., which can improve the comfort, safety, and reliability of automobiles.
- Electronics Industry: It can be used to manufacture keys, seals, protective covers, etc. of electronic devices, which can protect electronic components and improve the waterproof and dust – proof performance of the devices.
- Daily Necessities Industry: It is also widely used in the manufacture of daily necessities, such as kitchen utensils, toys, stationery, etc., which can meet people’s needs for product aesthetics, practicality, and safety.
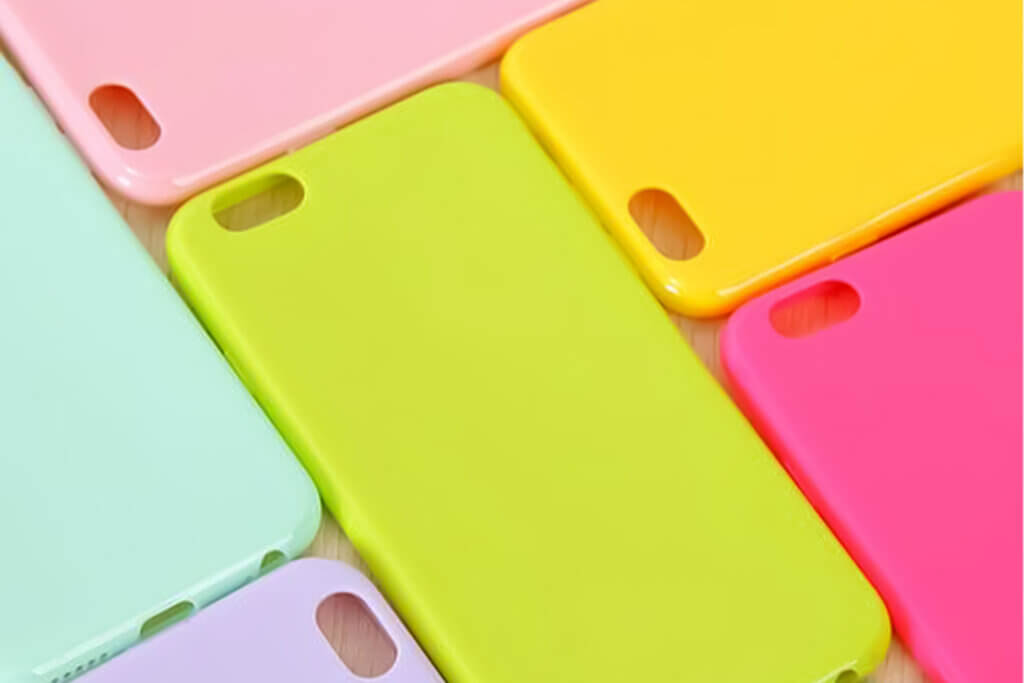
Design and Manufacturing Precautions for Liquid Silicone Rubber Injection Molding
- Product Design: In the product design stage, the characteristics of silicone rubber and the process requirements of injection molding need to be considered. The shape, size, and wall thickness of the product should be reasonably designed to avoid problems such as uneven wall thickness and excessive undercuts, so as to ensure the molding quality of the product.
- Mold Design: The mold design should fully consider the fluidity and curing characteristics of liquid silicone rubber, and reasonably design the gate, runner, and exhaust system to ensure that the liquid silicone rubber can smoothly fill the mold cavity and avoid defects such as bubbles and short shots.
- Process Parameter Control: The process parameters in the injection molding process, such as temperature, pressure, speed, etc., have an important impact on the quality of the product. The process parameters need to be precisely controlled according to the product requirements and the characteristics of the silicone rubber to ensure the stable quality of the product.
- Raw Material Selection: Selecting the appropriate liquid silicone rubber raw materials is the key to ensuring product quality. It is necessary to select silicone rubber with corresponding characteristics according to the use environment and performance requirements of the product, and pay attention to the quality stability of the raw materials and the reputation of the supplier.
Differences between Liquid Silicone Rubber Injection Molding (LIM) and Compression Molding
- Molding Principle: Liquid silicone rubber injection molding injects liquid silicone rubber into the mold cavity through an injection molding machine and cures under the action of pressure and temperature; while compression molding puts solid silicone rubber raw materials into the mold, applies pressure to make it flow and fill the cavity in the mold, and then heats and cures to form.
- Production Efficiency: Injection molding has a high degree of automation, a short production cycle, and high production efficiency; compression molding requires more manual operations, has a relatively long production cycle, and low production efficiency.
- Product Precision: Injection molding can produce products with high dimensional accuracy and good surface quality; compression molding is affected by the mold structure and operation, and the product precision is relatively low.
- Applicable Products: Injection molding is suitable for manufacturing various complex – shaped and high – precision products; compression molding is suitable for manufacturing products with simple shapes and large sizes.
Summary
As an advanced processing technology, liquid silicone rubber injection molding has many advantages and plays an important role in many industries. With the continuous progress of science and technology and the continuous growth of market demand, the liquid silicone rubber injection molding technology will also continue to develop and improve, providing stronger support for the development of various industries.
If you have any other questions about the liquid silicone rubber injection molding process or need to know more information about this aspect, you are welcome to communicate with us at any time.