Since its invention in the 1930s, silicone rubber has evolved significantly. It now comes in hundreds of grades and forms, catering to a vast array of applications that were unimaginable at its inception. Thanks to its remarkable properties like excellent temperature resistance, flexibility, and chemical inertness, the demand for silicone products continues to surge across various industrial, consumer, and medical markets.
Four Main Types of Silicone Rubber
1. Room Temperature Vulcanized (RTV) Silicone
RTV silicones are unique as they don’t require heat to cure into their final form. There are two sub – types: one – component (RTV – 1) and two – component (RTV – 2) formulations.
- RTV – 1: This type is ready – to – use straight out of the container. Once applied, a stabilizing agent within the silicone reacts with moisture in the air, starting the curing process from the outside. Different cross – linking agents are used, some of which release small amounts of acetic acid, amines, or alcohols during setting, while others are odorless. RTV – 1 is highly regarded for its ease of application, strong adhesion, and stability at high temperatures. It’s commonly used as sealants, bonding glues, and coatings.
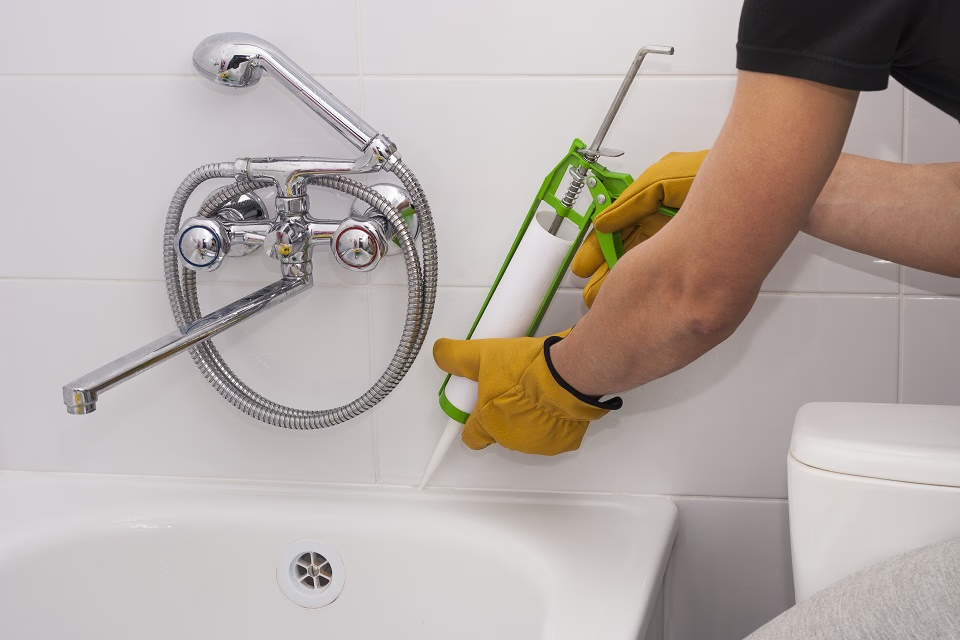
- RTV – 2: As the name implies, RTV – 2 comes in two parts that need to be mixed immediately before use. It cures more rapidly than RTV – 1 once the components are combined. RTV – 2 offers a broader range of products with exceptional mechanical properties across a wide temperature spectrum. Condensation – cured RTV – 2 is more budget – friendly compared to the platinum – cured version. Platinum – cured silicone is advantageous as it produces no by – products, making it suitable for specific applications. RTV – 2 finds applications in 3D printing, coatings, and mold making.
2. Liquid Silicone Rubber (LSR)
Liquid silicone mainly refers to the starting material used in manufacturing silicone products. In contrast to earlier semi – solid, gummy silicone grades that required compression molding, LSR is a two – part, platinum – cured raw material with excellent fluidity. This high fluidity enables it to capture intricate details in injection – molded components or conform precisely to any surface when used as a coating. The platinum – curing cross – linking system of LSR doesn’t generate any by – products during curing, making it an ideal choice for food – grade and medical – grade applications.
3. Fluorosilicone
Fluorosilicone is a modified form of the polysiloxane (silicone) molecule. It retains the basic silicon – oxygen chain but has some of its methyl (CH3) groups replaced by trifluoropropyl groups. This modification endows fluorosilicone with enhanced resistance to challenging service environments, including fuel, oil, mineral spirits, toluene, and other organic solvents. Despite these improvements in chemical resistance, fluorosilicone maintains mechanical properties similar to conventional silicone. However, it doesn’t perform as well in hot air as standard silicone and is notably more expensive. Fluorosilicone is best suited for aerospace and automotive applications where exposure to fuels and other chemicals is a common concern.
4. High – Consistency Rubber (HCR)
Also known as “solid silicone” or “gum stock,” HCR consists of high molecular weight polysiloxane chains. It can incorporate various fillers to enhance specific properties such as hardness and heat resistance. HCR can be cured using either peroxide curing systems or platinum catalyst formulations, with the latter producing no chemical by – products during curing. Sold in bulk forms like bars, tubes, and cylinders for further processing, HCR is an excellent material for long – term implantable medical devices, automotive engine components, and numerous consumer household products.
Diverse Forms of Silicone
Silicone can exist in multiple forms, each with its own set of applications:
- Emulsion: Silicone emulsions are made up of silicone molecules suspended in a stabilized water solution. They are used as lubricants, release agents, and in cleaning and polishing compounds to improve spreadability and durability.
- Oil: Silicone oils are simple, linear polysiloxane chains that can slide past one another, providing lubrication. They serve as hydraulic fluids, lubricating oils, and raw materials for further processing.
- Liquid: Liquid silicone rubber, as mentioned earlier, is fluid enough for precision injection molding. It’s a two – part formulation mixed just before being injected into the mold. Applications include gaskets, potting for electronics, formed parts, and medical devices.
- Caulk: Caulk is a viscous, room – temperature vulcanizing form of silicone. It offers superior workability, adhesion, and durability.
- Resin: Silicone resins are typically thermosetting products with branching molecules that form densely cross – linked structures. They are used in adhesives, protective and water – repellent coatings, and heat – resistant paints.
- Grease: Silicone grease is created by adding fillers to silicone oil. This thermally stable product lubricates surfaces, conducts heat, and protects against moisture and other chemicals. It’s used in mold release, glass joint seals, and electrical contact protection.
- Gel: Silicone gel is made from a two – part, platinum – catalyzed liquid formulation. It may contain additional oils or softeners to achieve the right consistency for forming thin sheets or packets. In the medical field, it’s used for scar reduction.
- Foam: Silicone foam is produced by adding outgassing agents to liquid silicone. This allows for the production of open and closed – cell foams with different densities. The foam can have a smooth surface for applications like gaskets and spacers or a rough surface for gap – fillers and pipe insulation.
- Solid: Solid silicone rubber, often referred to as HCR, has long polymer chains and high molecular weight. When cured, it’s relatively dense and hard and can be formed into products such as tubing, engine mounts, seals, and gaskets.
Classification and General Properties of Silicone
All forms of silicone fall under the category of non – organic elastomeric polymers. Silicones are known for their flexibility, non – reactivity, resistance to ultraviolet degradation, ability to maintain mechanical properties over a wide temperature range, and are generally considered non – toxic when used properly. They can be customized into various forms and tailored chemically to enhance strength, thermal stability, electrical conductivity, or chemical resistance, making them suitable for thousands of end – uses.
Liquid Rubber and Silicone: What’s the Difference?
A liquid rubber sealant can be based on silicone or other materials like polyurethane. “Liquid Rubber” typically refers to thin sealants applied to large areas such as driveways, roofs, and underground cement walls. On the other hand, “Liquid Silicone Rubber” (LSR) specifically denotes silicone. LSR is the raw material used for injection molding, joining and bonding surfaces, and sealing applications.
If you’re looking to produce high – quality silicone components, it’s crucial to choose the right composition and manufacturing techniques. For assistance, you can contact an industry expert or check out reliable quoting tools. There are companies that offer a wide range of manufacturing capabilities and value – added services for prototyping and production needs. You can visit their websites to learn more and request a free, no – obligation quote.
Disclaimer: The information provided in this article is for informational purposes only. While every effort has been made to ensure its accuracy, no representation or warranty, express or implied, is made regarding the completeness, accuracy, or validity of the information. Specific performance parameters, tolerances, design features, material qualities, and processes should not be assumed to be representative of what will be delivered by suppliers. Buyers are responsible for clearly defining their part requirements.