Custom Liquid Silicone Rubber Molding Service
Our liquid silicone rubber (LSR) molding process produces custom prototypes and end-use production parts in 15 days or less. We use aluminum molds that offer cost-efficient tooling and accelerated manufacturing cycles, and stock various grades and durometers of LSR materials.
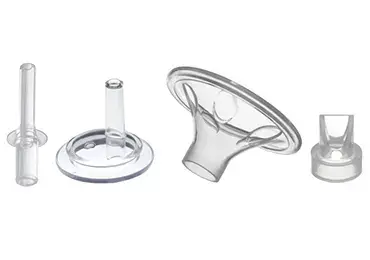
Start A New LSR Quote
STEP | STP | SLDPRT | IPT | PRT | SAT files
- All uploads are secure and confidential.
/01
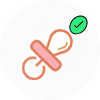
High Quality Parts
Our state-of-the-art laser cutting machines ensure precision in every project. Rigorous quality control guarantees that your custom metal parts meet exact specifications, delivering flawless results with every order.
/02
Fast Lead Time
Experience industry-leading speed with our project delivery. Our efficient online system and streamlined production processes reduce wait times, ensuring you receive laser-cut parts quickly and maintain your competitive edge.
/03
Engineering Support
Our engineering team turns design challenges into practical solutions. We offer hands-on support to ensure your custom laser cutting projects receive expert technical advice and design optimization, delivering superior results.
What is Liquid Silicone Rubber Injection Molding?
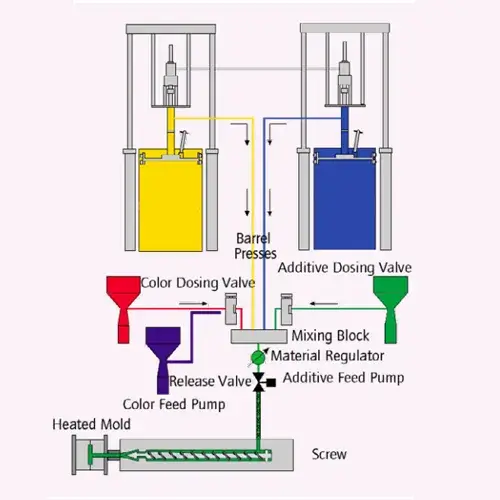
Liquid silicone rubber injection molding is the process used with liquid silicone rubber (LSR) to fix the material from an uncured state into a cured products.
Liquid Silicone Rubber (LSR) can be processed in a liquid injection molding (LIM) process. The liquid raw material is mixed from two separate components in a ratio of 1:1 and injected via a cold-runner system into a hot mold. Curing takes place within seconds, offering the advantage of fast cycling and the production of large quantities.
Injection molding of liquid silicone rubber (LSR) is a process to produce pliable, durable products in high volume (It is better at least 10000pcs/color). Then there will be have the cost advantage.
LSR elastomer offers exceptional optical clarity, durability, and design flexibility while maintaining excellent mechanical properties across a wide range of temperatures (-50oC to 250oC).
Shenghui’s Liquid Silicone Rubber Injection Molding uses these processes to ensure every component meets industrial standards.
Liquid Silicone Rubber Injection Molding Solutions
Prototyping
Rapid Tooling
Get easy design feedback and validation through superior quality prototype tooling. Create small batches of liquid silicone molded parts with excellent injection molding prototypes. We excel at manufacturing prototype molds within days to ensure you perform functional tests and validate market interest.
Production
Production Tooling
Liquid Silicone Rubber Injection Molding Manufacturing Network
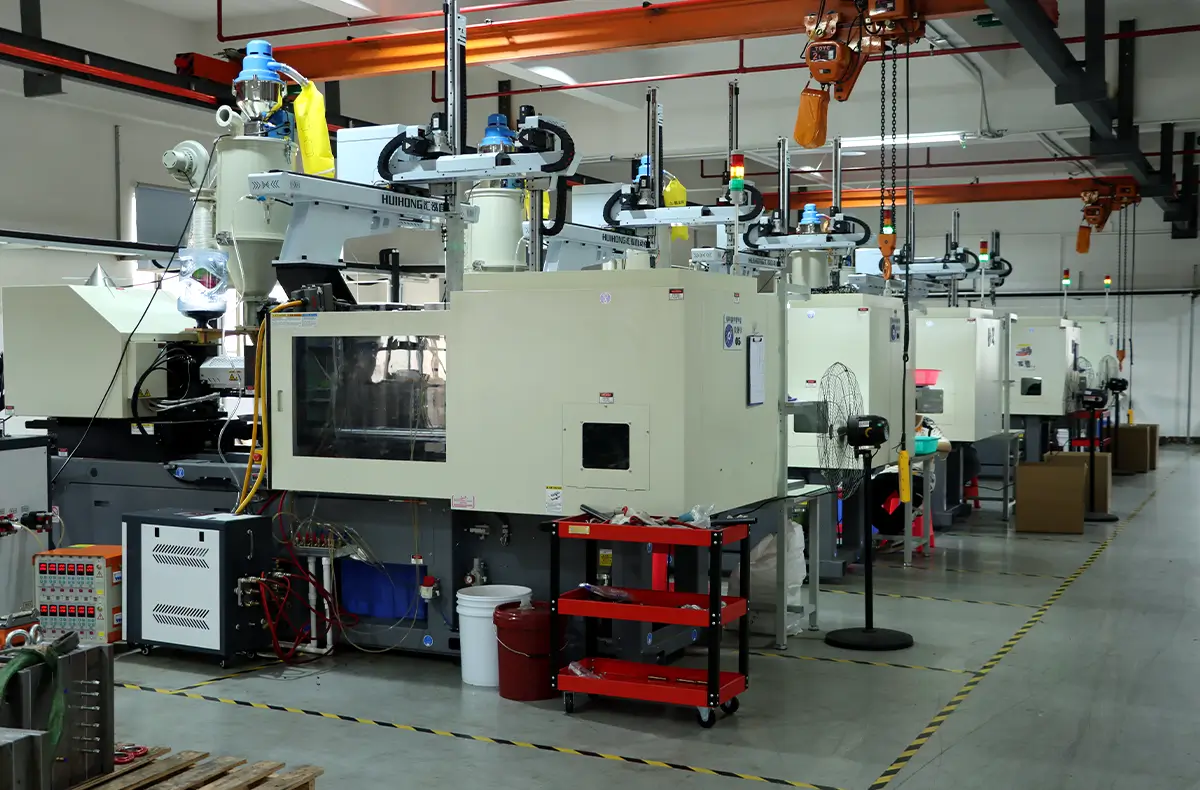
Equipped with over 30 advanced machines, capable of handling up to 400 tons, our network seamlessly manages projects from prototypes to full-scale production parts. Each engagement starts with a detailed injection mold quote to set clear expectations. Our project managers specialize in comprehensive manufacturing analysis and offer consultative design services to optimize each product for cost-effectiveness and functionality. The process concludes with detailed quality reports, ensuring all components not only meet but exceed industry standards.
materials
Liquid Silicone Rubber Injection Molding
We offer a wide range of silicone materials specifically chosen for their performance characteristics and suitability for compression molding applications.
Silicone
- Standard Silicone (30, 40, 50, 60, and 70 durometers)
- Medical-Grade Silicone
- Optical-Grade Silicone
- Fluorosilicone (fuel and oil resistant)
Liquid Silicone Rubber Molding Capabilities
ShengHui’s custom Liquid Silicone Rubber services ensure the creation of plastic parts that look and perform better. Our production line consists of an Liquid Silicone Rubber injection molding process that allows us to combine several different materials into one, ensuring you get superior-quality products.
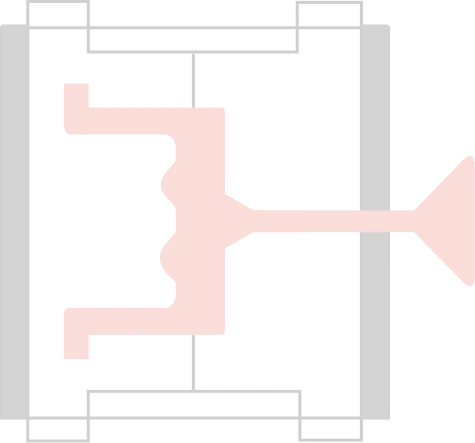
US | Metric | |
SIZE | 12 in. x 8 in. 4 in. | 304.88mm x 203.2mm x 101.6mm |
VOLUME | 13.3 cu. in. | 217,948 cu. mm |
DEPTH | No greater than 2 in. from any parting line; deeper parts are limited to a smaller outline | No greater than 50.88mm from any parting line; deeper parts are limited to a smaller outline |
PROJECTED MOLD AREA | 48 sq. in. | 30968 sq. mm |
Liquid Silicone Rubber Mold Surface Finishes
Our expertise also extends to providing SPI finishes for plastic silicone molds that enhance the aesthetics and functionality of your plastic molded parts.
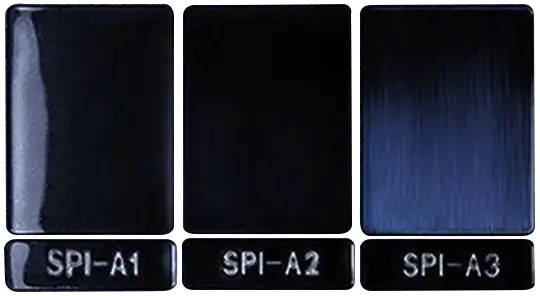
SPI A
Finishing Look | Matte |
SPI Finish Grades | SPI A1, A2, A3 |
Surface Roughness Ra (µm) | SPI A1: 0.012 to 0.025
SPI A2: 0.012 to 0.025
SPI A3: 0.05 to 0.10 |
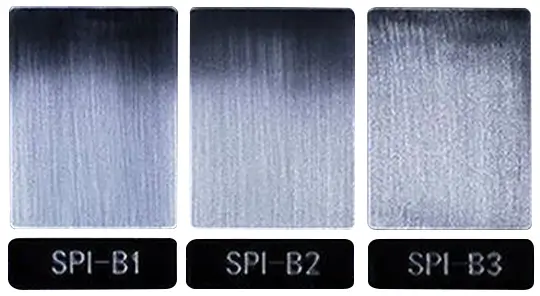
SPI B
Finishing Look | Matte |
SPI Finish Grades | SPI B1, B2, B3 |
Surface Roughness Ra (µm) | SPI B1: 0.05 to 0.10
SPI B2: 0.10 to 0.15
SPI B3: 0.28 to 0.32 |

SPI C
Finishing Look | Matte |
SPI Finish Grades | SPI C1, C2, C3 |
Surface Roughness Ra (µm) | SPI C1: 0.35 to 0.40
SPI C2: 0.45 to 0.55
SPI C3: 0.63 to 0.70 |
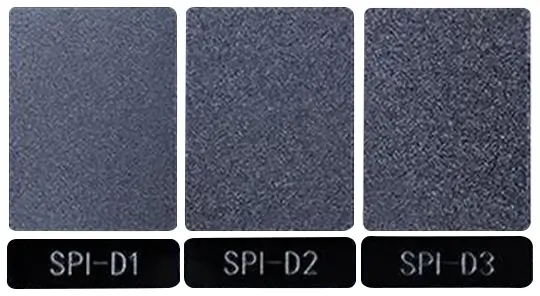
SPI D
Finishing Look | Matte |
SPI Finish Grades | SPI D1, D2, D3 |
Surface Roughness Ra (µm) |
SPI D1: 0.80 to 1.00 SPI D2: 1.00 to 2.80 SPI D3: 3.20 to 18.0 |
Liquid Silicone Rubber Silicone Molding for Various Industries
No matter the industry, our liquid injection molding systems enable the creation of high-performance liquid silicone rubber parts and components designed to endure harsh conditions, enhancing the effectiveness and reliability of your products. These solutions are ideal for a wide range of industries and applications, including:
Advantages of LSR Molding
Silicone Injection Molding can reduce assembly and labor costs, enhance part strength and reliability, and allow the integration of multiple materials and complex components.
- High production rates and shorter production cycles (results in lower per unit cost);
- Allows for close tolerances in small intricate parts;
- Requires little post-production work because parts have a finished look upon ejection;
- Full automation is possible, which leads to reduced production costs.
Applications of LSR Molding
ShengHui’s liquid injection molding cells produce durable LSR and LSR 2k parts for various industries:
- Automotive: Custom LSR components like connector seals, sensor parts, key fob membranes, vibration cushions, and HVAC system seals.
- Life Sciences: High-volume seals, gaskets, valves, and diaphragms for medical devices, drug delivery components, and wearable healthcare monitors.
- Industrial: LSR membranes and diaphragms in gas heaters, and seals for safety products like smoke detectors.
- Consumer Products: LSR parts in kitchen, bathroom, and personal hygiene products, as well as audio devices like headphones and speakers.