Silicone is an incredibly interesting material with a wide range of applications. It exists in various forms, such as oil, rubber, resin, and gel. No matter if you’re in the kitchen, looking for a reliable spatula, or handling a DIY home improvement project, like filling gaps in your bathroom or around windows with sealant, silicone is likely to be involved.
This remarkable material came into being in the early 1900s. F.S. Kipping played a crucial role in its discovery. He combined polydiphenylsiloxane (Ph2SiO, where Ph represents phenyl, C6H5) by drawing an analogy with the formula of the ketone benzophenone (Ph2CO). Initially named silicoketone, it later got a more appealing name – silicone, and eventually, the scientifically more accurate term siloxane.
What Is Silicone?
Silicone is a unique polymer. Unlike many others, it’s composed of siloxane chains. To form it, an oxygen backbone chain is required, with two organic groups attached to each silicon center. Methyl is almost always part of its organic group composition. The structure can be cyclic or polymeric. By adjusting aspects like chain lengths, cross-linking, and side groups, silicones with diverse properties can be created. In terms of texture and appearance, silicone offers a vast array of options. It can be an ultra – liquid substance, a rubbery material, a gel – like compound, or even a hard plastic. Silicone oil, also known as polydimethylsiloxane (PDMS), is very common.
How is Silicone Produced?
The production of silicone starts with extracting silicon from silica and passing it through hydrocarbons. Then, it’s combined with other chemicals. The rubber form of silicone has an inorganic Si – O structure with attached organic functional groups. The strong bond between silicon and oxygen gives silicone excellent resistance to high temperatures and the ability to stay flexible across a wide range of temperatures. After obtaining the silicone polymer, it’s blended with fillers and additives to form a stiff gum. Next, through cross – linking at a high temperature, with the help of peroxides or polyaddition curing, it transforms into a solid elastomeric material – silicone.
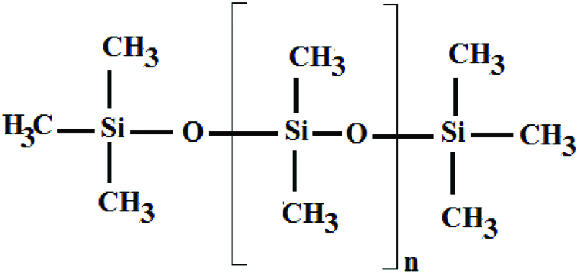
Silicone vs. Silicon: What’s the Difference?
It’s important to clarify that silicone and silicon are often confused, but they are distinct substances. Silicon is a chemical element, while silicone is a material that contains silicon along with other components.
The Properties of Silicone
Silicone has some outstanding physical and chemical properties. It can withstand extreme temperatures, from as low as -150°F to as high as 550°F before becoming brittle or melting. It’s highly flexible, with a tensile strength ranging from 200 to 1500 PSI and a maximum elongation of around 700%. Silicone is excellent at compressing and rebounding. It’s also resistant to heat and flames, and it bonds well with metals, making it a popular choice for adhesives and sealants. For outdoor products, it’s a great option as it can endure bad weather, and it has strong resistance to UV rays, water, and ozone. Additionally, it’s gas permeable, non – stick, and stain – resistant, which is why it’s widely used in the food and beverage industry as well as the medical sector. However, it’s not without its drawbacks. Over time, it’s not very resistant to oil (although some varieties offer slightly better resistance), and it can be prone to abrasion and wear.
Different Types of Silicone
There are numerous types of silicone, each with its own advantages:
- Methyl groups (MQ): These are among the earliest basic silicone rubbers. They form the foundation for many silicone – based products.
- Methyl vinyl groups (VMQs): If you need a material that can compress extremely well, methyl vinyl silicones are a great choice. The vinyl in this silicone makes vulcanization easier, and they are very common in various applications.
- Methyl phenyl (MPQ) and methyl phenyl vinyl (PVMQ) groups: What sets these types of silicone apart is their enhanced properties, especially their ability to maintain performance in cold temperatures.
- Flouro, vinyl, and methyl (FVMQ) groups: These silicones are better at handling oils, solvents, and fuels, making them suitable for specific industrial applications.
- Silicone rubbers: There are three main subtypes – liquid, room temperature vulcanized (RTV), and high temperature vulcanized (HTV). Liquid silicone has the shortest molecular chains, making it ideal for extrusion or injection molding, especially for weather – resistant products. RTV silicone rubber solidifies at room temperature and is commonly used for sealants, potting, and molds. HTV silicone rubber consists of long – chained polymers with high molecular weights. It usually comes as an unprocessed material and requires vulcanization at the same temperature as traditional rubber.
In the manufacturing process, silicon injection molding is a popular method. It uses a two – part resin combination that is dispensed from a mixing pump into a pre – heated mold set at 250 to 300 degrees Fahrenheit. After cooling, the final part is ejected from the mold. This method has several benefits, such as the ability to produce medium – to high – volume parts with shorter cycle times compared to compression molding. Also, due to the use of flash rings, vent tracks, and runner systems, there’s little to no flash to trim. It can even mold around threaded inserts, eliminating a labor – intensive post – molding process.