Silicone is an incredibly versatile synthetic material with a wide range of applications across numerous industries. It can be found in various products in our daily lives, such as the cars we drive, food preparation and storage items, baby bottles and pacifiers, as well as dental and other personal hygiene products. Silicone is also widely used in life – saving products like respiratory masks, IV devices, and other crucial medical and healthcare equipment. This article will delve into the production process, practical uses, and significant advantages of silicone, and also compare it with silicon and plastic.
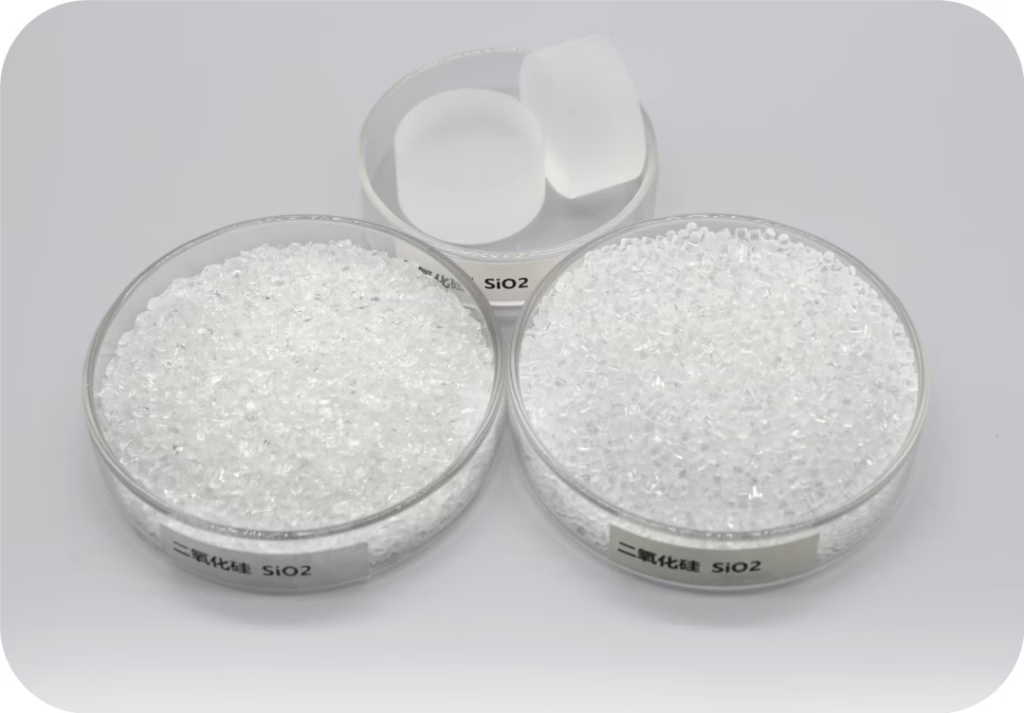
What is Silicone?
Silicone, also known as polysiloxane, is a man – made material. It is a polymer composed of siloxane, featuring a rubber – like texture. Its molecules consist of alternating silicon and oxygen atoms in a chain structure. This unique polymer serves as a key component in: resins, fluids, and elastomers. A notable difference between silicone and other industrial polymers is that the molecular backbone of silicone does not contain carbon. Silicone has a broad range of common applications, including lubricants, hydraulic fluids, water repellents, O – rings, heat – resistant seals, caulks, flexible molds, surgical implants, gaskets, electrical insulators, windshield wipers, shock absorbers, and sealants. It is utilized for diverse purposes in industries spanning from automotive and textiles to consumer goods and medicine.
What is Silicone Made of?
As a versatile polymer, silicone is used in caulks, oils, elastomers, and greases. The primary raw material of silicone is silica, which is one of the most common forms of sand. It’s essential to understand the differences between silicone and silicon.
What’s the Difference Between Silicon and Silicone?
Despite their similar spellings, silicon and silicone are produced differently. Silicon is a chemical element with the symbol Si. Like most elements, it does not occur naturally in its pure, isolated form. In contrast, silicone refers to a broad category of polymers that contain a siloxane bond (chemical formula -Si – O – Si -) attached to various organic compounds. They also vary in physical properties. Silicon is harder and more brittle, while silicone is softer, more flexible, and has better heat – resistant properties. Common applications of silicon include alloys, semiconductors, transistors, electrical insulators, bricks, photovoltaic cells, and computer chips.
How is Silicone Produced?
Step 1: Extract Silicon from Silica
The first step in silicone production is to isolate silicon from silica. To do this, a large quantity of quartz sand is heated to temperatures as high as 1800 degrees Celsius. The result is pure, isolated silicon. After it cools down, manufacturers grind it into a fine powder.
Step 2: Mix the Powder with Methyl Chloride
The fine silicon powder is combined with methyl chloride. Heating the mixture initiates a reaction that forms methyl chlorosilane. Methyl chlorosilane is a mixture of several compounds, with dimethyldichlorosilane being the most abundant and the main building block of silicone.
Step 3: Distill the Mixture
Converting dimethyldichlorosilane into silicone requires a complex distillation process to separate the components of methyl chlorosilane. Since chlorosilanes have different boiling points, this step involves heating the mixture to a series of precise temperatures.
Step 4: Add Water
After distillation, adding water to dimethyldichlorosilane causes the formation of hydrochloric acid and disilanol. The hydrochloric acid then acts as a catalyst for disilanol, causing it to condense into polydimethylsiloxane.
Step 5: Polymerize the Silicone
Polydimethylsiloxane contains a siloxane bond, which forms the backbone of silicone. The polymerization of silicone can be achieved through various methods, depending on the desired properties of the final product. Although the silicone production process may seem intricate, it is relatively straightforward in practice. It can be carried out on a large scale at a relatively low cost, which is why silicone, with its wide range of uses, has become one of the most popular elastomers in commercial and industrial applications.
Silicone vs. Plastic
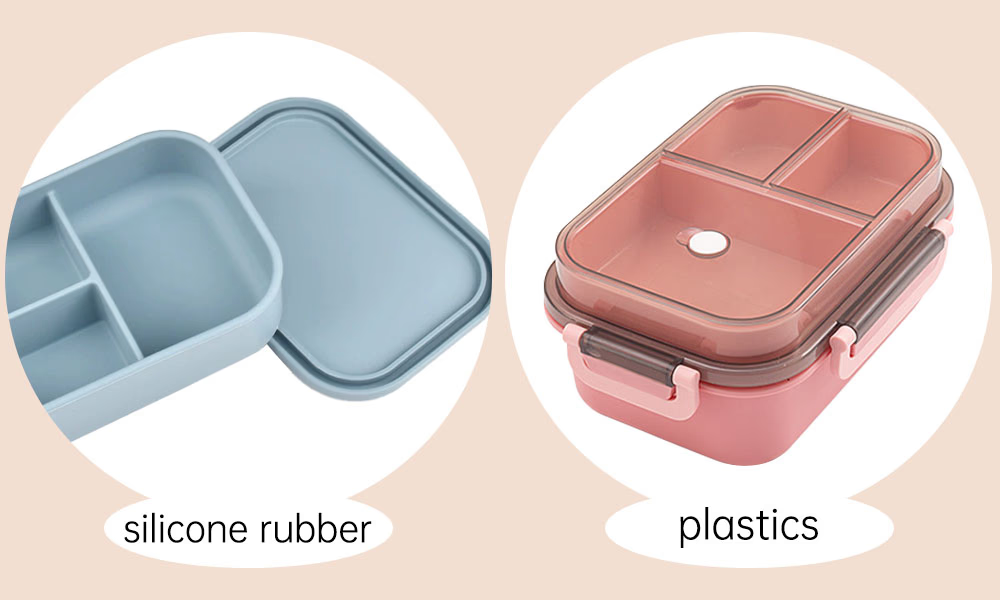
Plastic and silicone are both durable and malleable materials, and they may have a similar appearance and feel. However, their distinct chemical and molecular compositions set them apart. Plastics have a molecular backbone made up of carbon and hydrogen. They are produced from resources such as natural gas, plants, and crude oil. These raw materials are less environmentally friendly, and plastics can break down into harmful microplastics during decomposition. Some plastics also contain toxins like bisphenol A. Compared to silicone, plastics generally have a shorter lifespan and are less resistant to extreme temperatures.
Advantages of Silicone
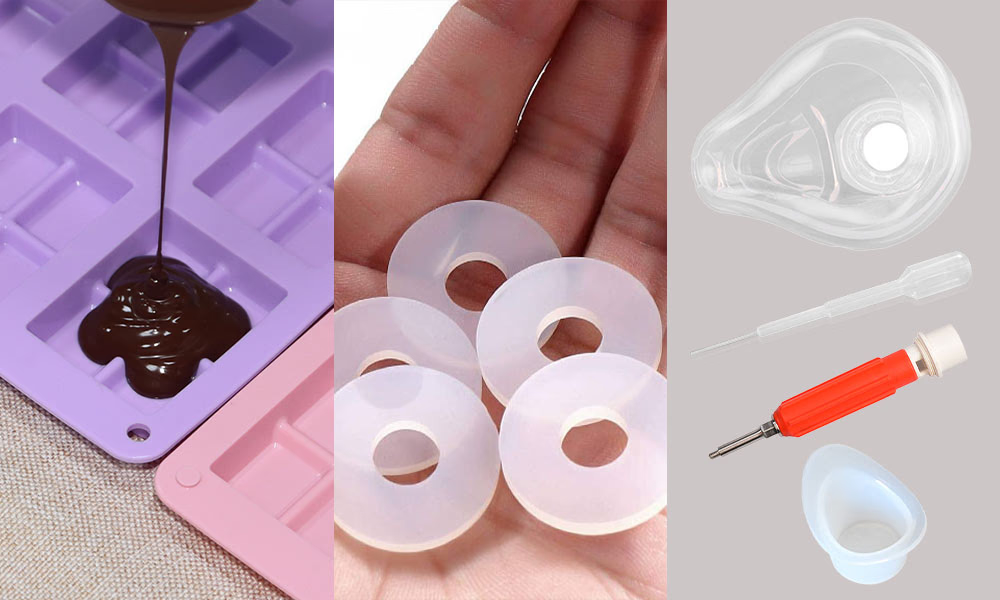
Silicone offers significant advantages in numerous applications. It has a variety of excellent properties, including flexibility, malleability, high clarity, temperature resistance, water resistance, air permeability, durability, easy cleaning, non – stickiness, stain resistance, high gas permeability, long – lasting performance, non – toxicity, and odorlessness. Silicone is easy to customize and mold, and it can be in the form of liquid, solid, or sheet, depending on the molding or manufacturing process and specific usage requirements. Regardless of whether an application demands higher heat resistance or greater malleability, material manufacturers can provide a variety of compounds and grades to meet different needs.
If you’re looking for high – quality liquid silicone rubber molded components, Dongguan Shenghui Silicone Rubber Products Co., Ltd. is your ideal choice. We are committed to providing customers with value – added solutions. We select the most suitable materials, molds, and manufacturing processes to produce high – performance liquid silicone rubber injection – molded parts, ensuring excellent results. Our liquid silicone rubber injection – molding units are equipped with precision automation equipment, innovative technologies, follow stable production processes, and implement strict quality standards, inspections, and tests. We customize products according to your specific requirements to achieve the highest quality level. We always strive to provide precise and value – added liquid silicone rubber components that continuously meet customers’ goals in production efficiency, cost control, and quality.